Shop by Category
Preventative Maintenance
Field Service & In-House Repair
All World’s service team of mechanical engineers, electric engineers and trained technicians are committed to fast, cost-effective repairs and innovations for your mechanical setbacks. We have the capabilities to build, rebuild, install, calibrate, upgrade, design, integrate, automate or retrofit your machine to get it up and running again.
Below, we will highlight the steps in our thorough preventative maintenance process.
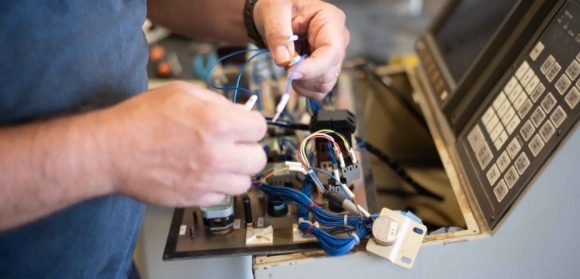
Inspection & Analysis
A specific and detailed checklist will be complete for each machine model.
Accuracy testing
Condition of level (pre & post)
Backlash report (pre & post)
Electrical components
Ball screws
Spindle oil cooler
Main spindle
Lubrication system
Tool changer
Cable carriers
Ways & wiper
Pallet changer
Axis check
Coolant system
Hydraulic system
Chip conveyor
Limit switches
All rollers
Counter weight chain
Flexible conduit
Project Scope
- Physical overview of each machine's condition prior to preventative maintenance date (pre inspection)
- Complete accuracy testing of machine
- Alignment problems identified during accuracy tests are correct (upon request, additional cost)
- PM service typically takes anywhere from 8 - 16 hours per machine (these time estimates may vary depending upon the specifics of the machine)
Action Plan
PM Pre-Inspection
A physical overview of the machine's current conditions; including a thorough pre-inspection checklist. Preceding this initial inspection, you will receive a detailed list of all components that are recommended for replacement.
PM Inspection
- Machine is cleared of any debris and way covers are removed
- Accuracy testing is preformed; including alignment checks of spindle and all axes
- Any faults identified during performance testing processes are corrected (backlash, axis alignment and machine level)
- Proper functionality of lubrication and oil delivery systems is confirmed (fluids will be exchanged if necessary)
- Electrical analysis and adjustments are completed
- Previously unexposed wipers on all axes are inspected (replacement upon request, additional cost)
- Operation of machine systems are analyzed
- Belts, pulleys, limit switches, proximity switches, pressure switches, motors, etc.. are adjusted and wear items may be replaced where necessary (replacement upon request, additional cost)
Post PM Review
- PM Checklist review with maintenance coordinator
- Results of PM are compared with previous records. This process will help to highlight any consistent issues that may directly affect machine performance. Future service recommendation will be made at this time.
Results
- Reduction of unscheduled downtime
- Improved geometric accuracies
- Benchmarking and maintenance records for each machine (these records will reduce the man-hours for subsequent machine PMs)
Schedule
All World Machinery Supply, Inc. recommends preventative maintenance be performed approximately every 6 to 12 months. (schedule can be adjusted according to hours of service)